The challenge of hearing protection
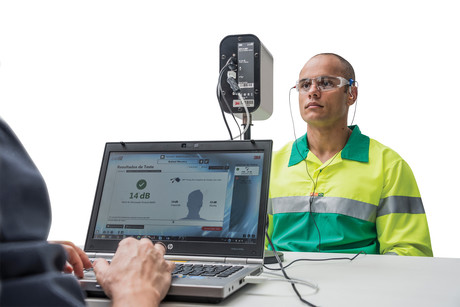
How do you know if your workforce is protected?
Protecting workers from hazardous noise levels is an ongoing challenge for many organisations. In fact, the most commonly recorded occupational health issue in the manufacturing sector is permanent hearing loss. The success of your safety program depends on many factors and requires more than just offering hearing protection.
E-A-Rfit™ is a service program designed to help validate hearing protection and compliance with hearing protection fit testing. It delivers an objective, quantitative measurement of each employee’s protection, so you can better protect your workforce while helping employees understand the importance of proper fit. With the E-A-Rfit Dual Ear validation system, your employees will learn how to properly fit their 3M earplug or earmuff, and you’ll have the confidence that they are wearing the right protection for their environment.
Individual fit testing using F-MIRE technology
Using F-MIRE (Field Microphone-In-Real-Ear) technology, the E-A-Rfit Dual-Ear Validation System generates a Personal Attenuation Rating (PAR) in under 5 seconds for both ears, taking into account the seven standard measured testing frequencies.
- Measures how well 3M’s most popular earplugs and earmuffs perform.
- Delivers a quantitative measurement of personal noise reduction for each employee.
- Can help identify whether or not the employee has adequate protection.
The right protection for your facility
Get results you can trust. The E-A-Rfit Dual-Ear Validation System measures the effectiveness of the hearing protection from inside the employee’s ear, providing accurate, quantitative results. And because you can simultaneously test both ears, you’ll have more time to educate employees on the importance of fit and compliance.
- FIT: Have the employee insert their earplugs or put on their earmuffs.
- TEST: Connect to microphones and begin speaker test sound.
- ASSESS: Use PAR to customise hearing protector selection.
Employee-to-employee variability
To make sure they are getting the protection they need, you need to know the PAR of every employee. The highest attenuating earplug or earmuff won’t provide the expected protection if it doesn’t fit right or isn’t used right. Once you know each employee’s PAR number, you’ll be on the way to yours: 100% confidence in your hearing conservation program.
Every employee is different. Every job is different. Every ear is different.
Finding each employee’s PAR number will help you validate compliance and have assurance that their hearing protection is sufficient.
It starts with PAR
The measurement of attenuation for a fit tested hearing protector is displayed as a PAR. To be sure that your employees are getting the protection they need, you should know the PAR of every employee.
Hearing protector ratings such as the noise reduction rating (NRR), the single number rating (SNR) and the sound level conversion (SLC80) are derived from measurements gathered in a carefully controlled laboratory environment. Although the ratings are an accurate measurement of the capabilities of a particular hearing protector under the specific test conditions, they may not represent what an individual worker will achieve when the device is worn. Most employees receive adequate protection, while some may not if they are not using the hearing protector correctly or have not chosen the correct size or style.
How much protection do employees need?
Each employee’s target PAR is based on the company exposure limit and the employee’s exposure. For example, if Employee A has a time-weighted average (TWA) exposure of 95 dBA and the company exposure limit is 80 dB, then the employee must receive a PAR of at least 15 or above in order to “Pass”. If the employee achieved 10-dB PAR, then the measurement will display “Fail”.
Example: 95 dBA TWA - 80 dBA Company Exposure Limit = 15 dBA Target Minimum PAR.
So, a 10 dBA PAR result is a “Fail” for this worker in their working noise environment.
How often should you fit test?
Much like audiometric testing, hearing protector fit testing is not a one-time event. Ideally, all employees in your hearing conservation program should be initially fit tested. For those who required extra training and/or a new size or style hearing protection, early follow-up is recommended to be sure the employee has access to the newly assigned hearing protectors, is wearing the usual or newly assigned hearing protectors and the device is continuing to provide adequate protection. Annual Hearing Protection Device (HPD) fit testing can provide assurance the hearing protectors are being worn correctly and give additional opportunity for further hearing conservation training.
How is fit testing conducted and where?
The physical location for testing may vary depending on your company but implementing fit testing is more efficient and effective if:
- the fit-test location is centrally located and easily accessible to the workers;
- managers and supervisors are engaged in the process and can assist in assuring the workers can leave their workstations to be fit tested quickly and on a timely basis;
- a flexible schedule with individual time slots is employed;
- a ‘wrangler’ is designated who can assist and ensure the efficient flow of workers to be tested;
- educational materials and tools are available if additional training is required;
- a complete selection of hearing protector samples of all types that are used at the plant is available to give to workers, especially for cases in which they have been ‘reassigned’ a different size or style based on fit test results.
Why use the 3M E-A-Rfit Dual-Ear Validation System?
Incorporating fit testing within a hearing loss prevention program results in a multitude of benefits.
The list below highlights the most compelling reasons why you should use the 3M E-A-Rfit Dual-Ear Validation System.
- Identify workers with low PARs who are consequently at risk for developing noise induced hearing loss.
- Verify the performance of HPDs without relying on laboratory-derived labels and derating schemes that are intended for groups of employees and not individual workers.
- Train and motivate employees on the proper use and fit of HPDs.
- Select and assign HPDs based on noise exposures, expected protection levels and the anatomy of the worker’s ear canal.
- Train personnel responsible for teaching employees the proper use and fit of HPDs.
- Provide a useful standard-threshold-shift (STS) follow-up procedure that can be used to determine whether the problem may be related to either the fit or the attenuation capabilities of the HPD.
- Provide data that may be accepted by regulatory agencies as a better alternative to using labelled attenuation values and derated to assess HPD adequacy.
- Audit departments to evaluate overall HPD effectiveness and suitability.
- Provide potentially useful documentation to demonstrate hearing loss prevention efforts conducted by a company that go beyond regulatory requirements.
Program documentation
E-A-Rfit Dual-Ear Validation System testing sessions produce a validation document that can be kept in each employee’s file, providing documentation of your commitment to training and compliance with Australian and New Zealand standards.
- Features easy-to-read test results for both ears as well as testing history.
- Creates digital and printable reports for both employee and company records.
- Provides a direct measurement of noise reduction in decibels.
- Provides an estimate of test variability.
Discover ATG®'s Industry-Leading MaxiFlex® Glove Range
Advanced Comfort, Dexterity and Protection with the MaxiFlex® Series of gloves by ATG®
MaxiCut® Ultra™ with AD-APT® - 52-4745D, 52-6745F, 52-6745FI
ATG's MaxiCut Ultra with AD-APT gloves are designed to provide exceptional cut resistance,...
Stay Cool and Comfortable with ATG's AD-APT® Technology in MaxiFlex®
ATG® has integrated its revolutionary AD-APT® Technology into the renowned MaxiFlex®...