Looking Beyond Clause 58: Modern Technology's Role in Mitigating Workplace Hearing Loss
By Julie Toseski, Occupational Hygienist and Application Engineer Specialist, 3M Personal Safety Division
Wednesday, 01 May, 2024
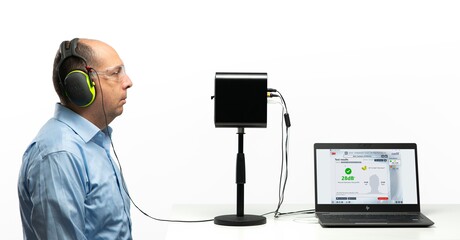
An estimated 1.1 million Australians are exposed to hazardous noise in their workplace, with occupational noise-induced hearing loss (ONIHL) being one of the most common, and preventable, occupational diseases. Despite legislative efforts, ONIHL remains a pressing concern, with no substantial decline in annual claims for workplace deafness over the past two decades.
In fact, across critical sectors, including construction, transport, and mining, temporary and permanent hearing loss is occurring without many workers’, or relevant Person Conducting a Business or Undertaking (PCBU)’s, awareness of the severity of this issue. The impact of this goes beyond the physical, with research even claiming people with severe hearing loss may be five times more likely to develop dementia.
Reflecting this from 1 January 2024, the NSW Government (through SafeWork NSW) commenced Clause 58 “Audiometric Testing” of the NSW Work Health and Safety (WHS) Regulation 2017.
Breaking down Clause 58 “Audiometric testing” of the NSW WHS Regulation 2017
From January 1, 2024, NSW PCBUs are now mandated to, “...provide audiometric testing to any of their workers who are frequently required by them to use… hearing protection… to protect the worker from the risk of hearing loss associated with noise that exceeds the exposure standard for noise.”
SafeWork defines audiometric tests as, “hearing tests… a painless, non-invasive test that measures a person’s ability to hear sound.” The tests measure a worker’s hearing threshold, establishing a baseline and monitoring changes over time, and determine shifts that could indicate temporary or permanent hearing loss. New workers need to be tested within three months of commencing work, and existing workers within two years of January 1, 2024. Workers will then be required to be re-tested every two years.
These assessments not only serve as a means of monitoring workers' hearing health, but also underline organisations’ commitment to prioritising employee well-being and fostering safety culture.
Protecting workers: the 3M™ E-A-Rfit™ Dual-Ear Validation Fit-Test System
Research indicates that irrespective of the chosen hearing protector, users must understand that even the most accurate hearing protection device (HPD) ratings merely offer a statistical approximation of the protection an individual might receive. Challenges like improper fitting techniques, temporary removal during work, and interference with other Personal Protective Equipment (PPE) can contribute to the subpar performance of these devices. Additionally, the misconception that higher attenuation properties equate to better protection can lead to overprotection, potentially compromising the audibility of essential communication and emergency sounds, thereby endangering workers' safety.
Unlike the laboratory-derived attenuation ratings (SLC80), Personal Attenuation Ratings (PARs) achieved through individual fit testing, provide insights into the specific attenuation a hearing protector offers an individual in real-world conditions. Fit testing also educates workers on comfort and fit, while emphasising the significance of actual protection achieved in the workplace and identifying training needs. By addressing issues related to hearing protection, it also supports improved safety compliance for employers.
Recognising advancements in fit testing technology, some Australian industries now mandate fit testing of hearing protectors to ensure optimal real-world attenuation and emphasise the importance of a proper fit in occupational hearing conservation programs.
The 3M E-A-Rfit Dual-Ear Validation Fit-Test System is one example of this advancement in fit testing technology. It uses science-based, objective, quantitative testing to measure workers’ unique PARs, empowering them to better fit their hearing protection PPE and safeguard their hearing health through active engagement. It tests both ears simultaneously in less than five seconds, works for earmuffs and plugs, tests at seven standard frequencies (125Hz to 8000Hz), and allows PCBUs to proactively keep a record of the hearing protection their workers are receiving.
Discover ATG®'s Industry-Leading MaxiFlex® Glove Range
Advanced Comfort, Dexterity and Protection with the MaxiFlex® Series of gloves by ATG®
MaxiCut® Ultra™ with AD-APT® - 52-4745D, 52-6745F, 52-6745FI
ATG's MaxiCut Ultra with AD-APT gloves are designed to provide exceptional cut resistance,...
Stay Cool and Comfortable with ATG's AD-APT® Technology in MaxiFlex®
ATG® has integrated its revolutionary AD-APT® Technology into the renowned MaxiFlex®...