Using wearable sensors to enhance safety and reduce injury
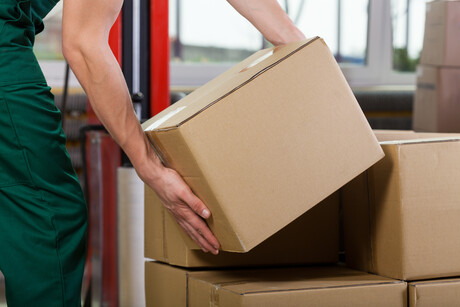
A leading manufacturer identified the role of Moulding as being at “high risk” of musculoskeletal injuries, as it inherently involves demanding postures unique to this role. Keen to address the manual handling requirements of this role, Jonesco (Preston) Ltd utilised dorsaVi’s technology to assess the role of Moulding and gain objective data to inform and reduce the risk of manual handling injuries. During the consultative session with dorsaVi, the team scoped the baseline assessment of the Moulder’s day-to-day tasks, as well as some specific comparative tasks. Jonesco broke down the key components of the role of Moulding, focusing on dexterous and heavy tasks, to isolate four areas which needed focus. These included XTB with and without Frekote (a versatile release agent), transferring the polymer, and one person versus two person demoulding.
During the onsite assessment, dorsaVi’s wearable sensors were attached to a Moulder who completed tasks within these four areas. The sensor captured the Moulder’s back and shoulder movements, including lumbar flexion, trunk inclination, pelvic angle (back), upper arm elevations (shoulders), and electro-muscular activity (back and shoulders). The dorsaVi assessor also used video throughout the assessment. To analyse the data, the sensor readings were synchronised with video footage to measure the postural and muscle activity risk factors. Utilising the data from the ViSafe assessment, Jonesco were able to implement some key practical changes for the role of Moulding. These included validating the benefits of using Frekote in reducing manual handling risk and updating their Standard Operating Procedures accordingly. Jonesco also investigated other similar products (such as using cooling agents) to reduce the manual handling risk and implemented conversations internally to identify alternative equipment and processes for transferring heavy materials to the moulds to reduce shoulder demand. Jonesco also implemented myViSafe small sensor and app technology to train and coach employees in best-practice manual handling techniques to drive behaviour change.
Overall, the objective data and results showed that the Moulder’s shoulders consistently scored a higher Movement Risk Score (MRS) than the back; due to the repetitive nature of the tasks, the large and awkward equipment utilised and the work environment, the Moulder was repetitively moving their shoulders into higher risk amber and red zones, indicating that this should be a focus for interventions and control strategies. Using XTB with Frekote reduced the overall MRS by 37.5% and improved efficiency by 65% (when compared to XTB without Frekote).
Using the ViSafe assessment, Jonesco gained insights into the role of Moulding, allowing the company to prioritise investments to maximise employee health and safety. With objective, visual data, management and employees had a clearer view of manual handling risks associated with certain jobs and a data-driven path to improve both behaviour and outcomes.
Boplan Impact Calculator for safety equipment
The Boplan Impact Calculator is an online calculation tool designed to empower safety...
Pack King powered floor cranes
Pack King powered floor cranes offer safety and efficiency for users.
Modulate portable buildings
Modulate portable building solutions offer flexibility and durability for demanding industries.