Reducing manual handling in a WA crushing plant
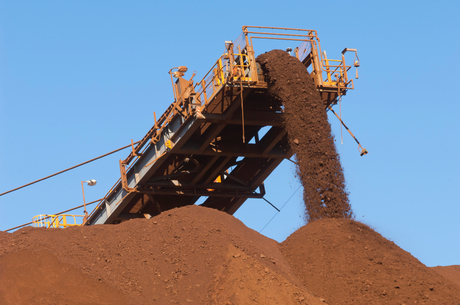
A Pilbara-based crushing plant in Western Australia has reduced its manual handling risks after implementing a wear liner system by Kinder & Co.
The company produces lightweight bulk materials handling componentry, engineered utilising composite polymer technology as a substitute to heavier steel or rubber constructed equivalents. The plant switched to the K-Superline Polyurethane Lining System, which has had multiple benefits, including reduced OHS hazards to workers.
The problem
The crushing plant provides contracting crushing and screening services to the mining industry and to control the feed to the screen, the conveyed material is put through a Schenk Vibratory Feeder. Due to the level of product build-up occurring on the existing plate chute lining (20 mm hardox 450), they needed to stop the plant and deploy resources 3-4 times per shift to jackhammer the iron ore manually. Additionally, given the impact from the 2.5 m drop height and the sliding abrasion, the existing conventional chute lining had to be replaced every 12 weeks.
The resolution
The K-Superline Polyurethane Lining System, specifying a B93 durometer hardness rating and 1″ thickness to suit the high levels of impact and sliding abrasion, was implemented at the plant.
The product has a low-friction surface that eliminated the problem of build-up and congestion through to the screen. This has stopped the need for any jackhammering on-site thereby reducing repetitive and physical labour for the workers.
The polyurethane also absorbs all of the impact of the crushed materials, which reduced the noise levels of the material being handled. Additionally, since the material is lighter than steel, the polyurethane was easier to carry and manoeuvre for workers when installing than the metal sheets previously used by the plant.
“Regretfully, one of the key reasons for the slow uptake of some of these OHS-friendly equipment solutions is that management overlooks the cost of OHS compliance,” said Neil Kinder from Kinder & Co.
“Instead they can be too driven by daily production targets at the expense of injuries to their human resources. What isn’t being considered is that short-term back pain can lead to more enduring and serious physically debilitating conditions.
“The situation then needs further financial investment to cover the salary costs of replacement contract workers,” he added.
The plant also reported around 50% more wear life after switching to the K-Superline Polyurethane Lining System.
Phone: 03 8587 9111
Boplan Impact Calculator for safety equipment
The Boplan Impact Calculator is an online calculation tool designed to empower safety...
Pack King powered floor cranes
Pack King powered floor cranes offer safety and efficiency for users.
Modulate portable buildings
Modulate portable building solutions offer flexibility and durability for demanding industries.