Proper Hydraulic Training minimising Injury Risk
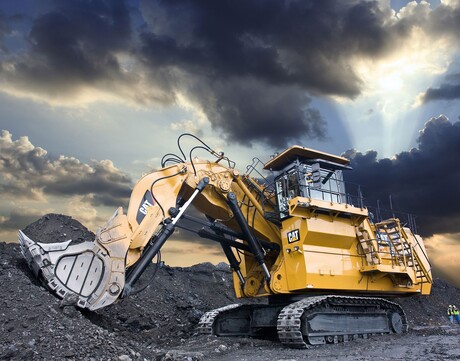
Almost all equipment used in the mining and industrial sectors are hydraulic-operated. Hydraulic transmission is one of the most efficient processes of transporting energy to perform repetitive mechanical movement such as lifting heavy loads, moving a piston, transporting incompressible fluids, with precise force control.
The nature of the hydraulic-powered equipment is they operate under high pressure and temperature. Hydraulic-operated equipment possesses an inherent ability to store multiple energy pockets. This stored energy must be safely dissipated from the process line during shutdown before any work is performed on the equipment. It is extremely important to follow appropriate safety measures to avoid accidents.
The need for regular maintenance intensifies as hydraulic components can wear out over time. Source of damages may include loose fittings, oil leaks, hydraulic fluid contamination, using non-suitable oil, improper storage and many more. Oil leak is one of the most commonly reported problems in hydraulic equipment which results from worn seals or damaged components. This leakage may promote premature failure of machinery, environmental damage, accidents which ultimately increases operational and capital costs.
Hazards Analysis in Hydraulic Equipment
If leaks are detected in the machinery, technicians perform troubleshooting to identify the source of leaks and fix the underlying issues. When untrained technicians perform this task, they may run their hands on the equipment to pinpoint the exact leak location. This is an extremely unsafe approach as it is one of the primary causes of a high-pressure injection injury.
High-pressure injection injury is defined as a stream of high-pressure fluids injected into your body. Hydraulic-powered machinery can exert an internal pressure up to 200 bar while a pressure of 7 bar is sufficient to break through your skin and damage the surrounding tissue. Therefore, a pinhole leak in hydraulic components could act like a hypodermic needle, injecting hydraulic fluid to the unsuspecting technician.
There are also many other incidents that may arise from handling high-pressure equipment, for example bursting of hydraulic accumulators. The accumulators must be safely de-energized before maintenance work is performed. A complete shut-off system does not indicate a safe “green-light” pass as there may be stored energy in the system. Diffusing this stored energy by bleeding to the atmosphere was previously documented as a familiar practice but it is actually a dangerous procedure. If not done correctly, the liquid bullets that arise from the procedure may propel the technicians to the air, resulting in severe injury or death.
Who should be trained in Hydraulic
An operator can have a decade-long experience in troubleshooting hydraulic equipment without proper training and qualification. The risk of accidents and injury can be dramatically decreased with proper training. Mandating every technician to get qualified hydraulic training will reduce this risk. However, will it be sufficient to train only the operators?
Let’s consider a hypothetical situation where a hydraulic technician has suffered an oil injection injury from troubleshooting a forklift. Oil injection injury looks like a small prick which may disguise the seriousness of the injury. The site supervisor will most likely advise the technician to get first aid and return to work if he/she is not aware of its consequences. Subsequently, the victim will experience progressively worse pain. By the time the technician is properly assessed at the hospital, the tissue around the injury site will have died. This preventable accident will have caused permanent disability to the victim.
If the site supervisor possessed good knowledge in hydraulic practice, they would have directed the victim to the hospital to receive appropriate treatment. The example above shows that the requirement of proper training extends to almost everyone that works on-site. This would ensure all personnel understand the correct management procedures to take appropriate actions when an accident occurs. Oil injection injury requires prompt and immediate treatment to debride the foreign material from the affected tissue to avoid tissue’s death.
Engineers that are involved in the design of the hydraulic system should also participate in the training. In most situations, technicians will refer to manufacturers’ guidelines on how to troubleshoot the equipment. The engineers must provide a safe working procedure on how to de-energize the system and maybe provide a guarantee that jet injection would not occur. If these instructions are missing from the guidelines, the maintenance technicians should not perform “bleed-to-atmosphere” procedures and instead, look for safer alternatives.
What is involved in hydraulic training
Introducing proper training as part of the technical orientation will enable operating engineers, technicians and on-site personnel to create a safe work environment. Trained operators understand the need to follow safety instructions before performing a task. They remain calm and understand how to act correctly when an incident occurs. Dealing with a safety-related incident with skills, knowledge and patience averts a potential accident and ensures that everyone can return home safely at the end of the day.
Training is generally delivered at the vocational school or registered training organization (RTO). Industries also have the opportunity to host an in-house by getting the required training equipment and qualified teaching instructors. While theoretical knowledge can be delivered in the classroom environment, students need to take practical exercises before performing real work. This practical module can be performed on a suitable demonstrator or hydraulic teaching equipment.
Hydraulic training equipment can be equipped with working components such as different types of pumps and valves with plug and play functionality. This configuration is intended to mimic the real-life experience and provide greater flexibility to teach every aspect of hydraulic fundamentals in both theoretical and practical manners.
The demonstrator should pose no safety hazards and has non-leaking components to suit classroom-style teaching. In addition, it should also allow the trainers to track and assess students’ performance to adhere to the teaching curriculum.
Looking Ahead
It is widely agreed for a company to maintain a safe working environment for accelerating growth and development. Companies that look to invest in their staff education, either through a collaborative partnership with training organizations or conducting in-house training, will reap the benefit in the foreseeable future.
Bestech has formed a collaborative partnership with the industry, university and training organization to support their course development activity by providing state-of-the-art technical training systems and local technical support. Our engineers and specialists are experts in bridging the gap between classroom learning and real-world experience. We prioritise the needs of customers and we support them by providing our expertise to develop long-lasting solutions.
From Safety to Security: Protecting Your Machinery in the IoT Era
For decades, Pilz has been a trusted partner in safety. Now, it extends that trust to security,...
See Beyond the Visible with the BodyGuard Pedestrian Safety Warning System
Protecting employees from potential collisions is a top priority for any busy facility.
Zoomlion Crawler Crane Breaks World Record for Lifting
What does it take to break a world record?