Using technology solutions to boost mine safety
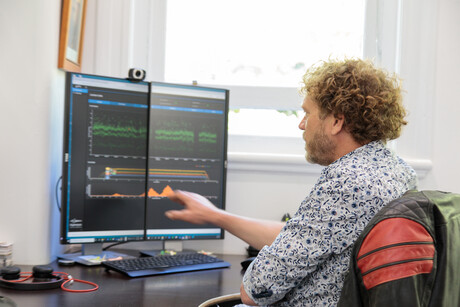
The mining and mineral processing industries face complex challenges and hazards that put workers, equipment, operations — and the environment — at risk. The integration of technology solutions (such as sensors and analytics software) and the effective planning and design of machinery, structures and processes can not only assist in risk mitigation, but also drive improved operational performance.
A local mine was experiencing faults on critical machinery within its processing plant, resulting in operational delays and unplanned downtime. To address this issue, the mine needed to determine the root cause of the failures and come up with an effective repair plan that could also be monitored for potential problems and proactively addressed if necessary to ensure worker safety.
The mine worked with the EngAnalysis team to create a monitoring system for the machine. The system utilised specialised analysis software which recorded structural stresses and identified operational cycles, and immediately analysed these for potential issues (for example, overloading or uneven loading) which could lead to failure. EngAnalysis also developed metrics on machine performance, fatigue and deterioration, to enable the engineers to track data trends and determine when intervention would be necessary during the operation.
“The early identification of potential safety hazards or design flaws through real-time monitoring and computational analysis of a prototype can allow issues to be addressed before manufacturing. This improves safety and operations, and minimises downtime by reducing equipment failure,” said John Vazey, Engineering Manager at EngAnalysis.
This approach also aligns with findings from McKinsey's 2022 report, ‘Navigating a Decade of Challenges: Five Winning Initiatives for Mining CEOs’, which emphasises the implementation of technology like sensors and machine learning in mines for enhanced efficiency, productivity and sustainability.
Equipped with the relevant data, a review of a new machine design was completed. The newly designed equipment was validated by instrumenting it with strain gauges and measurement tools and monitoring its performance for a period of time. The data gathered was then used to conduct a fatigue assessment and predict the equipment’s operational lifespan.
“The strain measurements in our processes enabled us to characterise the process behaviours that led to failures and unwanted downtime. With this insight, operators are now able to halt operations and adjust the load on the equipment, preventing structural failures and potentially lengthy periods of downtime,” Vazey said.
Through monitoring, data collection, analysis and design verifications and validations, EngAnalysis has provided the mining company with the confidence that the new equipment design will have an adequate fatigue life.
Technofast EziJac hydraulic tensioners
Technofast's compact multipurpose EziJac tensioners are designed to reduce complexity while...
Sphere Drones HubX unit for remote drone operations
The Sphere Drones HubX unit is designed to assist with remote drone operations, and is now being...
Volvo FH and Volvo FM trucks
The Volvo FH and Volvo FM trucks are designed to increase safety for drivers and road users.