Reducing hazards during mining haul truck maintenance
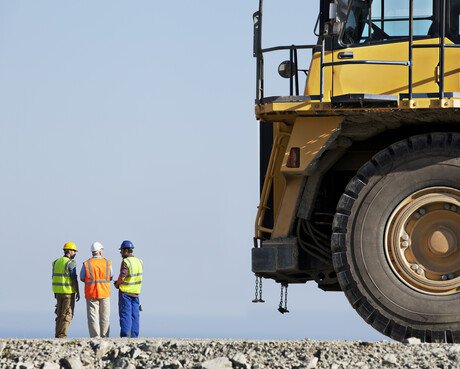
Haul trucks and dumpers are among the equipment that is most frequently associated with accidents within the mining industry.
According to the paper ‘Occupational Accidents Related to Heavy Machinery: A Systematic Review’, these accidents typically take place during repair and maintenance actions.
One of the main challenges in the mining industry has been ensuring the safety of maintenance personnel during the inspection and measurement of component wear on mining assets such as heavy vehicles. These tasks typically require technicians to physically be within the working envelope of operational vehicles to take manual measurements of moving parts, such as steering linkages during steering checks.
The traditional process for maintenance checks not only poses significant safety risks by placing personnel in the ‘line of fire’, it is also time-consuming, with little opportunity for productivity gains.
With mining companies seeking a solution that eliminates the need for workers to undertake these manual measurements during this heavy vehicle maintenance, Applied Measurement Australia paired its sensors with the T24 wireless transmitter from wireless measurement expert Mantracourt to create the XTRAN Telemetry Measurement System (XTMS).
“We were approached by some of the largest mining companies in Australia to help them eliminate live work around large vehicles,” said James Eccleston, Director of Business Development at Applied Measurement Australia. “The task was to come up with a solution to remove the need for maintenance technicians to be near or under the vehicles while they were operational, enabling them to safely capture necessary measurements from a distance.”
Traditionally, securing a haul truck for inspection required a lockout system involving a padlock for each maintenance worker operating on and around the asset, often necessitating the presence of three to five key holders to lock the truck, ensuring it remains immobile for safety.
During these maintenance inspections, workers would use traditional manual gauges, such as dial gauges, to take measurements on various moving parts to determine the amount of component wear. Manual inspections would typically involve three or more maintenance crew.
In addition to putting maintenance workers at risk of injury or fatality, the time taken to set up and capture a single measurement could be around 30 minutes or more. With numerous measurements to take during each asset inspection, this unnecessary set-up time can add up to many hours. Furthermore, the reading and recording of manual gauge measurements can be subject to human error, potentially leading to unexpected component failure or injury.
The deployment of the wireless telemetry system in mining operations has helped to improve both safety and maintenance, with one company reporting more than a 40% reduction in live work risk across their site, according to Applied Measurement Australia.
Since the successful development of the solution, Applied Measurement Australia has seen the deployment of over 100 XTRAN Telemetry Measurement Systems to mining operations mainly in Australia, as well as in North America and Africa.
“Through collaboration with Mantracourt and our end customers, these results demonstrate the capability our solution delivers to enhance mining safety and operational efficiency,” Eccleston said. “The ability to perform critical maintenance checks without exposing technicians to potential harm has set a new standard in the industry, showcasing the invaluable role of technological innovation in safeguarding lives and optimising performance.”
Phone: 03 9874 5777
Technofast EziJac hydraulic tensioners
Technofast's compact multipurpose EziJac tensioners are designed to reduce complexity while...
Sphere Drones HubX unit for remote drone operations
The Sphere Drones HubX unit is designed to assist with remote drone operations, and is now being...
Volvo FH and Volvo FM trucks
The Volvo FH and Volvo FM trucks are designed to increase safety for drivers and road users.