How improved plant guarding reduces injuries
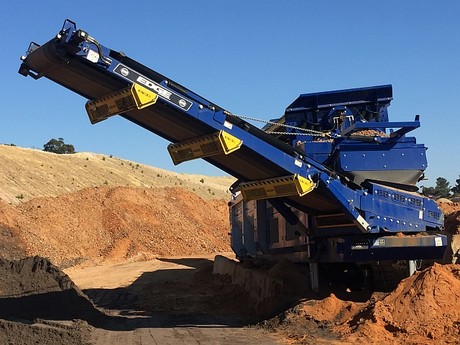
Serious injuries and even death can be attributable to plant machinery and equipment that have inadequate safety guarding.
WorkSafe Victoria conducted 106 visits to quarries during June to September 2017, and during this same period plant guarding was consistently flagged as a critical area for improvement.
Overall, a total of 44 plant guarding improvement notices were issued by WorkSafe Victoria, representing 39% of all notices issued.
Many bulk materials handling operators have now begun adopting a ‘zero harm’ approach in order to keep their workers, the environment and surrounding communities safe. This includes installing safety guards on machines and equipment to prevent injuries from occurring.
One plant operator in North East Victoria runs a large-scale gravel and sand plant, where site maintenance teams have reported ongoing guard maintenance due to the awkward and restricted access to many of its areas that require pinch point protection.
As well as protecting the workers from pinch point injuries, the maintenance team sought to implement safety guarding that was compliant with industry standard AS 4024.3610, and which would reduce cleaning downtime. The goal was to create opportunities for more proactive maintenance tasks within other parts of the plant.
The plant operator chose to implement Kinder Australia’s K-Protector Return Idler Guard to help reduce the potential for injury amongst its workers.
The K-Protector Return Idler Guard is industry compliant and a practical and safe solution to providing roller nip point protection. Its release mechanism is compliant and can easily and simply allow the safety guard to pass through the end plates for maintenance.
The unit is designed to minimise the potential for injury, with operators in all situations adhering to safe work practice procedures and avoiding adjustments to unlocked machinery.
After the safety guarding installation was carried out, the plant operator had positive feedback for the product. The site maintenance team said the solution was “easy and simple to fix to the existing brackets of our conveyor system”.
Safety guarding can be a significant investment for material handling operations. However, by incorporating guarding into ongoing maintenance programs in the long term, businesses are guaranteed worker safety, OHS compliance and extended wear life of equipment.
Kinder Australia suggests that an effective guarding maintenance program would check for some crucial considerations, such as those listed below:
- Safety guarding should be properly installed and all fasteners should be secure.
- Guards should be in good working condition; replacements should be considered if they are not.
- Guards should be free of corrosion.
- Replacement of worn or corroded parts, as needed, will extend the life of the guard.
Image courtesy of Kinder Australia.
Phone: 03 8587 9111
Sphere Drones HubX unit for remote drone operations
The Sphere Drones HubX unit is designed to assist with remote drone operations, and is now being...
Volvo FH and Volvo FM trucks
The Volvo FH and Volvo FM trucks are designed to increase safety for drivers and road users.
Isuzu safer vehicle cabin structure
Isuzu's reimagined vehicle cabin structure has been designed to improve overall safety,...