Forestry processing plant upgrade for control and safety
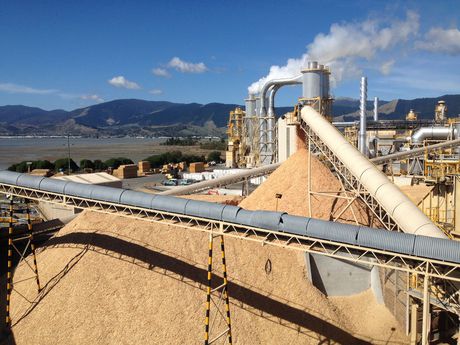
Nelson Pine Industries' plant in New Zealand operates 24/7 and has the capacity to process one million cubic metres of forest product per annum. As the ageing plant was in need of an upgrade, Nelson Pine called on Rockwell Automation to develop a solution that integrated control and safety while minimising production downtime.
The chip mill is a large part of the site where logs are unloaded from trucks for processing. Two pivot cranes and a drum debarker handle 300 tonnes of logs per hour. According to Ian Craw, automation engineer at Nelson Pine Industries, “To upgrade the chip mill we decided to start at the whole backbone of control to take advantage of advancing technologies and meet current safety standards.”
Control and safety are critically important in the chip mill so the first stage of the upgrade involved replacing the existing PLC-5 hardware platform with a GuardLogix Integrated Safety System.
According to Sean Doherty, account manager at Rockwell Automation, “The GuardLogix provides the benefits of the standard ControlLogix systems but also includes safety features that support Category 4/PLe safety applications. The GuardLogix also offers integrated safety, discrete motion, drive and process control.”
To allow for zone control, the chip mill building was split into two geographical safety zones, using some of the latest safety guard locking switches with RFID technology for controlling and monitoring zones.
The first safety zone incorporates a large drum debarker, which rotates the logs, removing bark before entering the chipper. Outdated variable speed drives were replaced with eight, 90 kW PowerFlex 753 drives in a master/slave configuration. They receive their speed/torque reference via the DLR and achieve a Stop Category 0 (via safe torque off) to Cat3/PLd.
“The integrated safety provided by zone control allows the plant to shut down one zone while the other is still operating as usual, delivering improved production rates. The goal is zero harm but we also wanted to minimise impact to production schedules so we suggested a solution that helps achieve this,” said Doherty.
The second safety zone incorporates safe speed monitoring of the main, 1.8 MW chipper motor and safe position monitoring of the 11 kV motor breaker, to confirm lockout/tagout (LOTO) has been performed, before access is granted into the hazard zone.
“When upgrading equipment it was a priority to meet current safety standards. We are well on the way to complying with the Machine Safety Standard, EN ISO 13849, with the goal to achieve PLd across most of the site in the coming years,” said Craw.
As there are many hundreds of metres between different parts of the site, an EtherNet/IP network was used to reduce both the amount of cabling required and the installation times, with fibre running the longest legs.
Using Device Level Rings (DLRs) achieved complete integration of the control and safety system; the ring topology provides high availability of the safety network with high resiliency. Various DLRs were run to different parts of the site connecting with field safety devices, bringing the information back to one centralised safety processor that monitors the various processes.
“One of the huge benefits of the solution is being able to have visibility remotely. We use PanelView Plus as the operator interface for fault finding and monitoring equipment out in the field. In our previous system we had to use multiple software systems to try to diagnose an issue, but now both the control and safety code are easily accessed and visible through ControlLogix,” said Craw.
In addition to the PowerFlex 753 drives, which are used on site, Nelson Pine is using the PowerFlex 525 drives with safe torque off and ethernet capabilities, reducing commissioning time and fault-finding time.
Nelson Pine Industries has adopted production processes that are both safe and environmentally sound. As a result of the success of the new control and safety solution in the chip mill, Nelson Pine is planning to roll out the solution across the entire plant.
Phone: 03 9757 1111
Technofast EziJac hydraulic tensioners
Technofast's compact multipurpose EziJac tensioners are designed to reduce complexity while...
Sphere Drones HubX unit for remote drone operations
The Sphere Drones HubX unit is designed to assist with remote drone operations, and is now being...
Volvo FH and Volvo FM trucks
The Volvo FH and Volvo FM trucks are designed to increase safety for drivers and road users.