Digital twin technology levels up construction safety
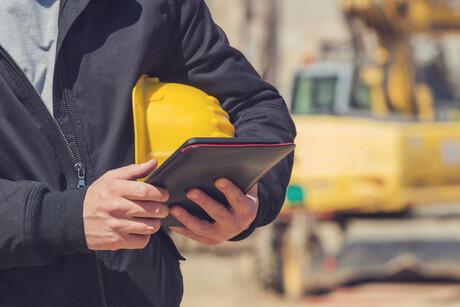
Safety on the modern construction site could be improved by implementing technologies like drones, laser scanners, virtual reality and the Internet of Things (IoT). Another emerging technology with safety benefits for the sector is the ‘digital twin’, which, when adopted, is predicted to shake up the construction industry like never before, according to a University of New South Wales (UNSW Sydney) construction management expert.
“A digital twin is a digital replica of a physical entity utilising Internet of Things enabling two-way communications between them,” said Dr Samad Sepasgozar from UNSW Built Environment. “At the strategic level, the digital twin is a new game-changing approach to construction automation … that will transform the industry quicker than ever before.”
The idea is that for every physical item in the world, there could be a virtual replica with which it connects, housed in the cloud, collecting vital data on the physical item’s performance in real time. “Industry players might confuse this with building information modelling,” Dr Sepasgozar said. “But unlike this previous technology, the digital twin also enables users to control equipment.” Digital twin technology enables job-site tasks to be performed remotely, which can be useful during disruptions like those caused by the coronavirus (COVID-19) pandemic. Dr Sepasgozar is developing a digital twin of an excavator, enabling improved diagnostics and analytics of the machine’s performance.
Excavator digital twin
“The digital twin and the physical excavator can communicate with each other, in real time,” Dr Sepasgozar said. “All the changes applied to one are applied to the other. For example, you can command the physical equipment and communicate with it [remotely]. On the other hand, the physical object will communicate with you so you can examine its performance, condition and productivity.” Users can use the data to learn how to increase productivity by changing the operation scenarios, the attachments of the equipment, or the distance between the equipment and the specific floor of a building.
A major safety challenge for construction management is operating equipment safely and controlling its downtime, according to Dr Sepasgozar. The digital twin can teach users how to evaluate hazards from the safety of afar and may remove the need to be present onsite altogether. “So, for example, if the operator is not experienced enough, you can use the digital twin from your office, and then you can command and operate the excavator [remotely],” Dr Sepasgozar said. “It’s an online app on smartphones, so it’s much easier to use than you think… In terms of visualisation, in terms of controlling or using it, it is much easier than any previous digital automation technologies.”
Digital twin technology could also be scalable to an entire construction site and facilitate simulation training exercises virtually to better prepare construction workers for the potentially life-threatening situations they may encounter. “It will cover all kinds of activities within a construction project — all of them, one day, will be connected to digital twins,” Dr Sepasgozar said. “We already have a lot of different types of sensors, drones and other tools which will contribute to developing an entire construction digital twin.”
Visualisation and communication
A digital twin is also a powerful tool for data visualisation and communication, providing the full picture of construction management with accurate, up-to-date datasets in a user-friendly format. Dr Sepasgozar believes that digital twins could also help to make the construction industry more accessible and equitable for smaller players by giving them a platform. “Most previous technologies, like building information modelling (BIM), are implemented by bigger guys in the industry,” Dr Sepasgozar said. “But [here] we are talking about smaller stakeholders, people on the ground level, family businesses, the subcontractors such as excavation contractors.” The appetite for digital twins could carry over into other relevant businesses, with Dr Sepasgozar suggesting that businesses that fail to adopt the technology could run the risk of being left behind.
“If you adopt this, the entire process of management and the automation process will be changed,” Dr Sepasgozar said. With broader innovations in machine learning and connectivity, Dr Sepasgozar predicts that an increasing number of real-life assets will have digital twin counterparts within the next few decades. However, the success of the digital twin will depend on construction users making the technology work for them. “From the user perspective at the construction projects level, it’s not only about who is going to dominate the market,” Dr Sepasgozar said. “We need to think about the user benefit if we’re going to make the technology a success.”
Sphere Drones HubX unit for remote drone operations
The Sphere Drones HubX unit is designed to assist with remote drone operations, and is now being...
Volvo FH and Volvo FM trucks
The Volvo FH and Volvo FM trucks are designed to increase safety for drivers and road users.
Isuzu safer vehicle cabin structure
Isuzu's reimagined vehicle cabin structure has been designed to improve overall safety,...