Developing a safe way to remove large underground raise bore reamers
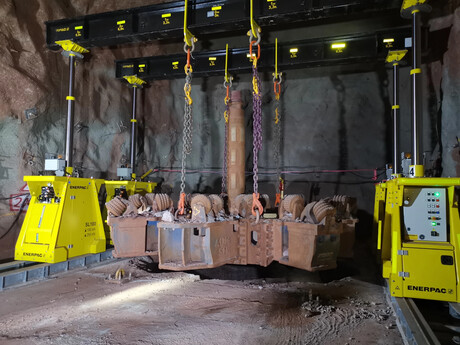
Raise bore beamers are used in underground mining worldwide to excavate a circular hole between two levels of a mine, without using explosives. The removal of raise bore beamers can be a hazardous, complex, costly and time-consuming process. Specialist underground mining contractor PYBAR Mining Services has implemented a safe and cost-effective initiative that can be applied globally, by using an Enerpac SL100 Hydraulic Gantry to provide a safe and efficient way to lift and position the heavy load, where traditional cranes would not fit and permanent overhead structures are not an option. This facilitates the removal of large diameter reamers safely in an underground environment. PYBAR Mining Services Raise Bore and Shaft Lining Manager Phillip Viljoen said that in the raise bore industry, there are two known methods of removing large diameter reamer heads, once the reaming of an underground shaft is complete.
“The first method is to lower the reamer head to the base of the shaft and use a thermal lance to cut the drill string and drag the reamer away from the hole, but this method exposes the worker doing the job to the possibility of falling rocks — a hazard that’s difficult to control. The second method is to install breast plates in the backs above the reamer head, at the top of the hole, and use air hoists to lift the reamer out of the hole. Steel beams are then placed across the hole, which the reamer is lowered down onto, dragged forward away from the hole, disassembled and removed. This method is time-consuming, expensive and complex in the controls required to ensure safe completion of the job,” Viljoen said.
Viljoen noted that the company has used the air hoist method before, but due to costs and the complexity of the job, the company worked with Enerpac to develop and safely test the SL100 Reamer Lifting Gantry System. Antony Cooper, Marketing Manager for Enerpac Asia-Pacific, added that the SL100 Hydraulic Gantry System was key in the success of removing the raise bore reamers in an underground environment, as it provided a more efficient way to remove large diameter reamers while enhancing safety at the same time. “The SL100 Hydraulic Gantry is operated remotely, with the Intelli-Lift wireless control system, which is included with all Enerpac hydraulic gantries. The Intelli-Lift controller offers superior safety and control by removing employees from the shaft area during reamer lifts. When the reamer is lifted out of the shaft, the reamer is trammed away from the open shaft, which is then covered with a hole cover to create a safe working area,” Cooper said.
Cooper added that skid tracks are essential to the safety and performance of the Enerpac Super Lift gantry range. Skid tracks, available in 3 and 6 m sections, are critical to setting up a gantry safely, as they reduce ground-bearing pressure and ensure the gantries are aligned during travelling. The cost-effective Enerpac SL-Series Super Lift Gantries provide high-quality control and high capacity utilising telescopic cylinders offered in two or three stages. The SL100 Hydraulic Gantry offers higher lifting capacities (up to 100 tonnes) than previously in gantries of this type, while providing accurate load positioning on a compact 610 mm track gauge. Designed for safe lifting in confined or limited-access spaces, such as underground mining applications, the SL-Series Gantries are easy to mobilise and demobilise. All Enerpac gantries are delivered with job-specific performance properties and control systems, for optimum safety and stability.
The gantries feature self-contained hydraulics, wireless Intelli-Lift controls, synchronous lifting and lowering, and self-propelled wheels or tank rollers with synchronised travel. The lift is controlled by the Enerpac Intelli-Lift wireless control system, which removes the need for workers to be near the shaft area and allows them to be in a safer location during the lift. The SL100 is designed and tested to meet ASME B30.1-2015 safety standards and is Lloyds witness tested to 125% of maximum working load for safe, reliable operation. In addition to comprehensive testing and safety features, the SL100 Gantry is backed in the field by Enerpac, which has 50 years’ experience in high pressure (700 bar, 10,150 PSI) hydraulic equipment. Enerpac has a global ‘Goal Zero’ initiative in which it strives for zero safety incidents to occur while using Enerpac tools worldwide.
Phone: 08 9414 0100
Technofast EziJac hydraulic tensioners
Technofast's compact multipurpose EziJac tensioners are designed to reduce complexity while...
Sphere Drones HubX unit for remote drone operations
The Sphere Drones HubX unit is designed to assist with remote drone operations, and is now being...
Volvo FH and Volvo FM trucks
The Volvo FH and Volvo FM trucks are designed to increase safety for drivers and road users.