Cloud Software Service for Managing Your MSA Portable Gas Detection Fleet
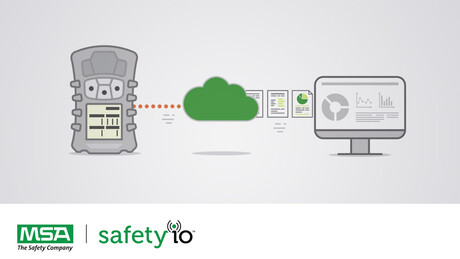
Grid Fleet Manager is a web-based service to streamline the gas detection fleet management by EHS management personnel such as safety managers and industrial hygienists. It helps regain control of their gas detection program so they can shift their focus to broader safety goals.
It helps them maximize their gas detector uptime and drive worker accountability from anywhere with an Internet connection via a Web browser. All data in transit is encrypted and secured in the virtual private cloud, and being monitored with AI-based anomaly detection for additional security. The data is backed up securely every hour.
A Software-as-a-Service (SaaS) subsidiary of MSA The Safety Company, Safety io combines over 100 years of safety equipment expertise with the speed and innovation of a software start-up. Amazon Web Services Internet of Things (AWS IoT) platform is leveraged to support the real-time services. Safety io has been recognized by Amazon for the innovative way in which this platform is utilized.
Although this type of service is not new to the industry, the approach to identifying and resolving customers’ safety pain points (via the deployment of intelligent and simple features supported by an intuitive user interface) makes it stand out from the other options on the market. It is also improved regularly based on customer feedback.
In addition to helping our customers both maximize their gas detector uptime and drive safer behaviours, it allows our customers to be far more efficient and effective in these efforts so they can be more proactive while shifting their focus to higher-value safety activities.
There is no report received in the last 12 months on how the service assisted the reduction of any occupational accidents or injuries. However, there is customer testimonial on how it helped a power company which used to spend nearly 100 hours on an unconnected gas meter system to prepare for an audit. The health and safety team is now empowered to streamline their gas detection program. Whether on or off-site, the team can confidently manage its detection program and know their coworkers are protected by detectors that are ready for duty.
The team can also better understand when and how gas detectors are being used to provide the best training and knowledge related to detector use. Compliance and world-class gas detection management is easier than ever, because of Fleet Manager’s integrated real-time data access, automated notifications of needed actions, ability to oversee a geographically spread out fleet of gas detectors and report sharing capabilities.
Information Access
- Receive a daily e-mail notification about your fleet’s status. Quickly discern what needs your attention and take action.
- Access your fleet information easily—at anytime and from anywhere.
- Find, download and share reports as you need them—calibrations, detector records or alarms.
Fleet Compliance
- Ensure your gas detectors are ready for work (bump tested, calibrated and with sensors functioning properly). Reduce downtime.
- Proactively decommission any equipment that requires maintenance.
- Understand which equipment are in use (by whom) and which ones are available.
Risk Assessment
- See the data from your devices and identify hazards your workers are exposed to.
- Understand the root cause of incidents and initiate preventive measures.
- Translate findings into quality and worksite safety processes and actionable workflows.
Worker Compliance
- Drive accountability for the equipment by assigning your fleet’s detectors to a company, department, and worker.
- Understand if the devices are being properly used and operated.
- Identify training opportunities based on equipment usage information.
About MSA
Established in 1914, MSA is the global leader in the development, manufacture and supply of safety products that protect people and facility infrastructures. Many MSA products integrate a combination of electronics, mechanical systems and advanced materials to protect users against hazardous or life-threatening situations. The company's comprehensive line of products is used by workers around the world in a broad range of industries, including the fire service, the oil, gas and petrochemical industry, construction, mining and utilities, as well as the military. Principal products include self-contained breathing apparatus, fixed gas and flame detection systems, handheld gas detection instruments, head protection products, fall protection devices and thermal imaging cameras. MSA, based north of Pittsburgh in Cranberry Township, Pa., has annual sales of approximately $1.2 billion, manufacturing operations in the United States, Europe, Asia and Latin America, and 42 international locations.
For more information, click here.
Enhancing Workplace Security with Master Lock's Bluetooth® Connected Locks and Lockboxes
Protecting valuable assets, restricting unauthorised access, and ensuring the safety of employees...
The importance of a strong safety culture during the pandemic
A strong safety culture is a key goal for any organisation, but with regulations putting more...
Safety and the sewage pumping station
Submersible pumping stations are convention, but not necessarily the safest option, nor the most...