Down to the wire
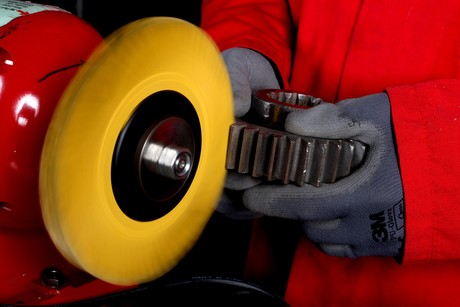
Wire brushes offer a relatively useful solution for surface cleaning and corrosion removal, but newly available alternatives are delivering superior performance and improved worker safety.
The challenge
The use of rotating brushes — composed of fine wire bristles that project from a metal wheel attached to an electric drill, backstand or bench motor — is commonplace for industrial tasks such as cleaning rusty metal or removing paint.
Despite offering reasonable levels of performance, the use of wire brushes in these applications puts workers at significant risk, as individual bristles are prone to break off during the process. These stray bristles then become airborne and can be easily embedded into the operator’s eyes or other body parts at high speed, with outcomes ranging from mild discomfort to serious and lasting eye damage. Common feedback indicates wires also embed themselves in the operator’s clothing causing injury away from the work area.
The problem is exacerbated when brushes are used at high revolution levels, whereby the bristles fan out and increase in diameter and, subsequently, in velocity. Medical journals are full of case reports on penetrating eye injuries caused by rotating wire brushes, which can require surgical procedures — such as traumatic cataract removal and lens implants — to rectify. The signs and symptoms of injury are often initially minimal — in many cases it presents only as blurred vision — leading the injured party to defer or entirely forgo medical treatment, running the risk of more serious and permanent damage.
Beyond potential projectile injury, the use of wire brushes also contributes to operator fatigue, as the user is required to exert a constant, even pressure to achieve the desired finish result.
Wire brushes also limit productivity; they contain no abrasive minerals, which makes it harder to achieve a suitable outcome; finishes are not easily repeatable, so it takes longer to complete the task; and, finally, it’s difficult to determine which brush will deliver the best results, requiring unproductive labour time to evaluate.
The solution
Advances in technology have allowed the development of nylon radial bristle brushes that can significantly diminish safety risk, while simultaneously improving performance.
The nylon bristle construction offers many benefits, particularly when it comes to worker safety. In the event of break-off, soft nylon bristles cannot penetrate the eyes or skin, even at high revolution levels. Appropriate PPE (such as eyewear and gloves) should always be worn.
Durable yet flexible, the patented brush bristle design delivers a continuous supply of a ceramic abrasive mineral that reduces the pressure required and therefore lessens the risk of operator fatigue. Designed to resist gumming and loading, the brushes can last longer and work quickly on both soft and hard metals to produce a consistent finish, making the overall job easier.
Performance testing shows that nylon radial bristle brushes cut faster and more efficiently than wire solutions. On materials such as mild carbon steel, they outperform .014 mil wire brushes by as much as 10 to 1 in cut rate testing. They do not require increasing pressure to optimise cut rates, minimising user effort.
The benefits
While the physical properties of a nylon radial bristle brush system make it suited to a broader range of applications and material substrates than wire brush alternatives, the benefits don’t end there.
Despite the best of intentions, safety managers must occasionally contend with PPE policy non-compliance. In opting to utilise a nylon bristle brush solution, even unprotected workers are unlikely to be seriously injured, adding a further level of safeguard against harm.
Nylon radial brushes are inherently more efficient at delivering repeatable results — and thanks to the inclusion of an abrasive mineral material that is designed to do all the work, operators are less susceptible to the fatigue that comes from exerting continual, even pressure.
For managers looking to significantly improve worker safety, while enjoying enhanced productivity and performance levels, it may be time to say “down to the wire”.
Phone: 136 136
HEMCO flammable storage cabinet
The HEMCO cabinet for flammable storage is specifically designed for the storage of flammable...
Clesana C1 water-free mobile toilet
The Clesana C1 water-free mobile toilet is being introduced to Australia by national distributor...
Lutz Pumpen modular canister pump tube
The Lutz Pumpen modular canister pump tube is designed to improve health and safety for workers.