Confined space working: how awareness & planning keeps operatives safe
By Andrzej Janowski, European Segment Marketing Manager, MSA Australia Pty Ltd
Monday, 02 November, 2020
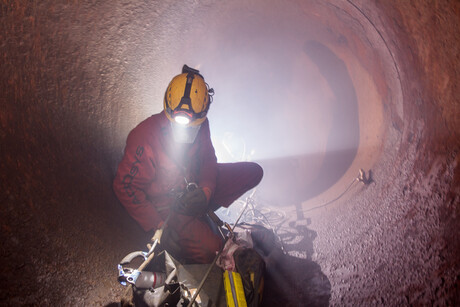
Working at height can present numerous safety risks. These must be carefully assessed, considered and mitigated with the correct fall protection systems, equipment and training. But what happens when operatives are faced with an added layer of complexity: entering a confined space to complete essential inspections or works? Andrzej Janowski, European Segment Marketing Manager for safety equipment manufacturer MSA, offers best practice guidance for carrying out confined space works.
Confined space working represents one of the most high-risk undertakings for any organisation. There are many potential dangers to workers, including injury or death from falls, physical entrapment in the limited space or poisoning/asphyxiation from noxious gases (to name just a few).
The accident statistics are sobering. IOSH reported in 2016 that around 15 workers a year in the UK lose their life in confined space accidents1. Causes can range from an inability to recognise the confined space and its dangers, inadequate systems for safe working, and ill-conceived rescue attempts. For instance, the US sees 670 confined space deaths a year and tragically, research by the US National Institute for Occupational Safety and Health (NIOSH) revealed that approximately 60 percent of confined space fatalities came from rescuers trying to assist and extract victims2. Fatalities in confined spaces can happen quickly in seemingly innocuous situations.
Europe adopts a risk-based approach which focuses on a case-by-case basis and puts the liability on the employer to identify the risk and take the appropriate measures. The European Union has not introduced any legislation specifically relating to work in confined spaces (with the exception of temporary or mobile construction sites). However, the Framework Council Directive 89/391/EEC of June 12, 1989 covers all aspects of safety and health at a workplace; as a result, the Directive places a duty on employers to consider the specific characteristics of every workplace (including confined spaces).
Under the risk-based approach, it is the employer’s responsibility to take appropriate measures to identify and manage the risks. Although this risk-based approach gives employers the freedom to determine how risks are managed, it also exposes corporate directors and facility managers to criminal liability should things go wrong.
Enhesa3, for example, has reported that several company directors or business owners have been found guilty of manslaughter. Similar cases were found in Belgium where directors faced prosecution and were sentenced to prison because of failure to take appropriate safety measures.
Understanding confined space environments
It may initially seem obvious, but the first thing to understand is whether the workspace is likely to pose risks associated with a typical confined space environment. In practice, a confined space is any environment that is not designed for continuous human occupancy. A space may be substantially enclosed, partially open, have limited access for entry and exit, and, once inside, it may present risk of serious injury because of hazardous substances or conditions. Written authority to enter a confined space and/or a permit of work is therefore often a legal requirement.
Whether carrying out inspections, ongoing maintenance or repairs, works in confined spaces are routinely a necessity in several sectors, especially for organisations engaged in delivering utility services, energy and transportation. Typical operations and activities include the provision of water and sewage handling; oil, gas and petrochemical production; shipping (within cargo vessels and dockyards); and mining.
Recognise, assess and test, plan ahead, monitor
The first step is for employers to confirm that supervisors and operatives are competent and fully recognise the hazards and unique risks of confined space works. This responsibility sits with the employer. There is no room for error: specialist safety and equipment training, and regular refresher exercises are absolutely essential. If the assigned team is not fully conversant with confined space procedures, the working method, the safety equipment and emergency rescue measures, the work simply must not proceed.
Thorough evaluation and testing of the confined space allows the team to understand the particular hazards, and deploy the appropriate safety equipment, checks and measures to help mitigate risk. Is the atmosphere inside the space dangerous? Lowering a probe into the space before entry will safely test the oxygen levels and reveal the presence of noxious gases such as hydrogen sulphide, carbon monoxide or vapours. If breathing apparatus is needed, what equipment is most suitable? Choices include running an airline down to the operator from a monitored surface-based tank or providing a self-worn (but bulkier) supply.
How will the space be accessed? If it is a vertical shaft, is there a risk of falling? Ensuring the correct equipment is in place for fall protection and, if needed, emergency extraction, including a fully trained operator above ground, is essential. If access is via a ladder, a secondary fall arrest device with a rescue provision may be sufficient; but if access requires the operative to descend suspended in a harness with a raise and lower device, a secondary fall arrest device and a rescue winch is called for. MSA, for instance, offers an easy to deploy tripod for vertical descent to 15m, and a winch solution reaching 30m.
It is a sad fact that written company procedures to do works often don’t adequately consider rescue of an operative who becomes trapped or could fall. Yet planning for the unthinkable can help prevent injury and death. There should always be a rescue procedure in place before any confined space works commence. Arrangements for raising the alarm and carrying out rescue operations in an emergency must be clearly agreed, documented and understood. The team must be able to execute extraction procedures correctly, without hesitation or doubt, if ever the need should arise.
The need for vigilance
Constant and vigilant monitoring above ground and communication with operatives during confined space works can help to reduce dangers and risks. For example, whilst oxygen levels may appear safe at higher levels in the space, heavy gases may reside further down in the structure. A gas concentration detector worn by the operator can continuously relay data through a smartphone app to the cloud for real time monitoring or trigger an alarm should conditions unexpectedly change or deteriorate.
Planning is key
One thing is certain when it comes to confined space working: planning is key. From risk assessments to rescue plans, all involved — whether that be supervisors or operatives — should be well-informed, well-prepared and properly trained. Regular practice is also often essential to comply with local regulations. This responsibility sits with the employer.
In Europe, MSA works with specialist external training partners. MSA provides its partners with training materials, training samples, and most importantly, the necessary training for its partners to deliver the courses. Extremely experienced and fully instructed in using and maintaining the equipment, MSA’s partners offer accredited courses including fall protection, and rescue and equipment inspection. For more information about fall protection requirements for confined spaces, and detection and protection solutions, visit:
Confined Space Entry: The MSA Difference
1. IOSH, Confined Spaces, The National Food and Drink Manufacturing Conference
MSA Safety launches award-winning ALTAIR io 4 Gas Detection Wearable device
The ALTAIR io 4 and MSA+ create a versatile hardware/software combination that enhances worker...
Ensuring the safety & accuracy of your gas detection instruments
Calibration is required to ensure that gas detectors are displaying an accurate measurement; it...
Staying cool: The cost of heat stress in the workplace and how big fans make a big difference
High volume, low speed (HVLS) fans can help cool off employees and improve efficiency for the...